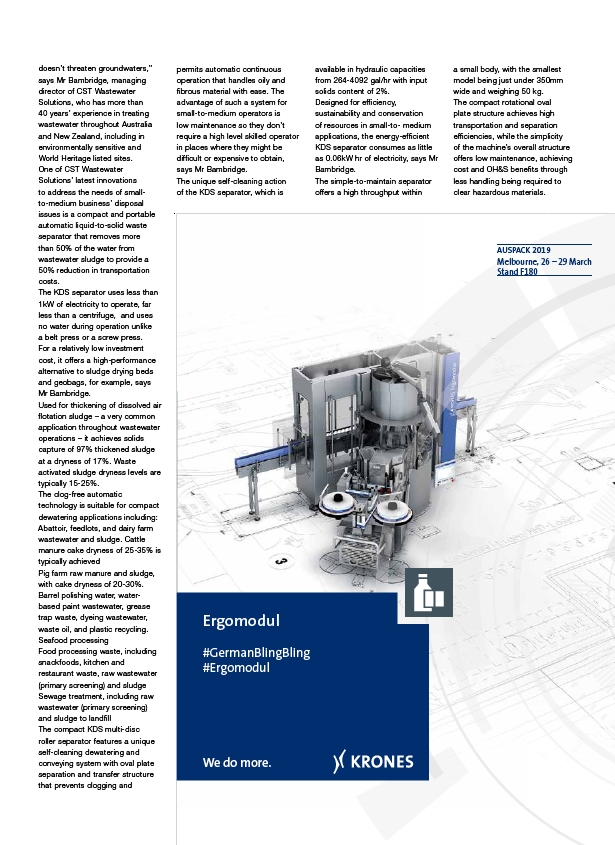
New Zealand Food Technology, 172 x 246 mm, Ergomodul, CC-en21-AZ119 02/19
Ergomodul
#GermanBlingBling
#Ergomodul
We do more.
AUSPACK
Melbourne, – March
Stand F
doesn’t threaten groundwaters,”
says Mr Bambridge, managing
director of CST Wastewater
Solutions, who has more than
40 years’ experience in treating
wastewater throughout Australia
and New Zealand, including in
environmentally sensitive and
World Heritage listed sites.
One of CST Wastewater
Solutions’ latest innovations
to address the needs of smallto
medium business’ disposal
issues is a compact and portable
automatic liquid-to-solid waste
separator that removes more
than 50% of the water from
wastewater sludge to provide a
50% reduction in transportation
costs.
The KDS separator uses less than
1kW of electricity to operate, far
less than a centrifuge, and uses
no water during operation unlike
a belt press or a screw press.
For a relatively low investment
cost, it offers a high-performance
alternative to sludge drying beds
and geobags, for example, says
Mr Bambridge.
Used for thickening of dissolved air
flotation sludge – a very common
application throughout wastewater
operations – it achieves solids
capture of 97% thickened sludge
at a dryness of 17%. Waste
activated sludge dryness levels are
typically 15-25%.
The clog-free automatic
technology is suitable for compact
dewatering applications including:
Abattoir, feedlots, and dairy farm
wastewater and sludge. Cattle
manure cake dryness of 25-35% is
typically achieved
Pig farm raw manure and sludge,
with cake dryness of 20-30%.
Barrel polishing water, waterbased
paint wastewater, grease
trap waste, dyeing wastewater,
waste oil, and plastic recycling.
Seafood processing
Food processing waste, including
snackfoods, kitchen and
restaurant waste, raw wastewater
(primary screening) and sludge
Sewage treatment, including raw
wastewater (primary screening)
and sludge to landfill
The compact KDS multi-disc
roller separator features a unique
self-cleaning dewatering and
conveying system with oval plate
separation and transfer structure
that prevents clogging and
permits automatic continuous
operation that handles oily and
fibrous material with ease. The
advantage of such a system for
small-to-medium operators is
low maintenance so they don’t
require a high level skilled operator
in places where they might be
difficult or expensive to obtain,
says Mr Bambridge.
The unique self-cleaning action
of the KDS separator, which is
available in hydraulic capacities
from 264-4092 gal/hr with input
solids content of 2%.
Designed for efficiency,
sustainability and conservation
of resources in small-to- medium
applications, the energy-efficient
KDS separator consumes as little
as 0.06kW hr of electricity, says Mr
Bambridge.
The simple-to-maintain separator
offers a high throughput within
a small body, with the smallest
model being just under 350mm
wide and weighing 50 kg.
The compact rotational oval
plate structure achieves high
transportation and separation
efficiencies, while the simplicity
of the machine’s overall structure
offers low maintenance, achieving
cost and OH&S benefits through
less handling being required to
clear hazardous materials.