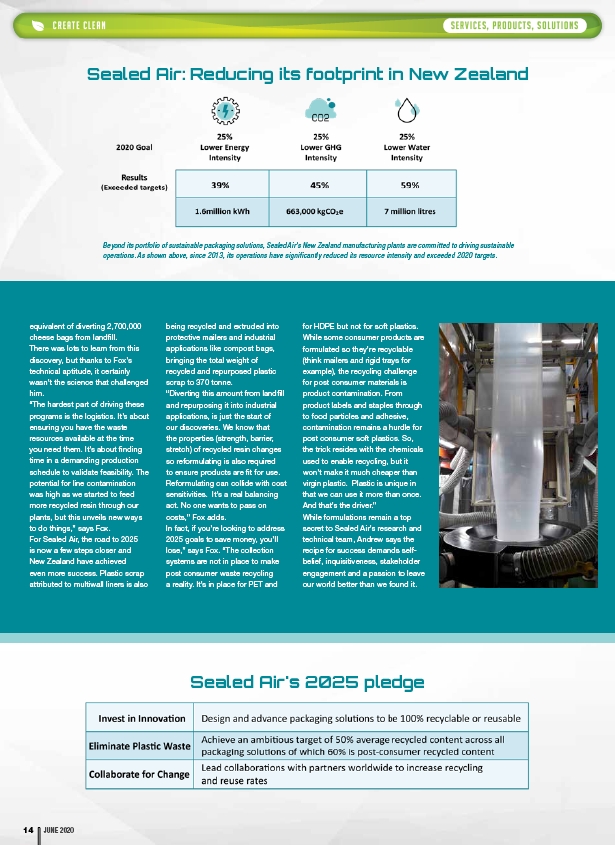
CREATE CLEAN SERVICES, PRODUCTS, SOLUTIONS
Sealed Air: Reducing its footprint in New Zealand
Beyond its portfolio of sustainable packaging solutions, Sealed Air's New Zealand manufacturing plants are committed to driving sustainable
operations. As shown above, since 2013, its operations have significantly reduced its resource intensity and exceeded 2020 targets.
equivalent of diverting 2,700,000
cheese bags from landfill.
There was lots to learn from this
discovery, but thanks to Fox’s
technical aptitude, it certainly
wasn’t the science that challenged
him.
“The hardest part of driving these
programs is the logistics. It’s about
ensuring you have the waste
resources available at the time
you need them. It’s about finding
time in a demanding production
schedule to validate feasibility. The
potential for line contamination
was high as we started to feed
more recycled resin through our
plants, but this unveils new ways
to do things,” says Fox.
For Sealed Air, the road to 2025
is now a few steps closer and
New Zealand have achieved
even more success. Plastic scrap
attributed to multiwall liners is also
being recycled and extruded into
protective mailers and industrial
applications like compost bags,
bringing the total weight of
recycled and repurposed plastic
scrap to 370 tonne.
“Diverting this amount from landfill
and repurposing it into industrial
applications, is just the start of
our discoveries. We know that
the properties (strength, barrier,
stretch) of recycled resin changes
so reformulating is also required
to ensure products are fit for use.
Reformulating can collide with cost
sensitivities. It’s a real balancing
act. No one wants to pass on
costs,” Fox adds.
In fact, if you’re looking to address
2025 goals to save money, you’ll
lose,” says Fox. “The collection
systems are not in place to make
post consumer waste recycling
a reality. It’s in place for PET and
for HDPE but not for soft plastics.
While some consumer products are
formulated so they’re recyclable
(think mailers and rigid trays for
example), the recycling challenge
for post consumer materials is
product contamination. From
product labels and staples through
to food particles and adhesive,
contamination remains a hurdle for
post consumer soft plastics. So,
the trick resides with the chemicals
used to enable recycling, but it
won’t make it much cheaper than
virgin plastic. Plastic is unique in
that we can use it more than once.
And that’s the driver.”
While formulations remain a top
secret to Sealed Air’s research and
technical team, Andrew says the
recipe for success demands selfbelief,
inquisitiveness, stakeholder
engagement and a passion to leave
our world better than we found it.
Sealed Air's 2025 pledge
14 JUNE 2020