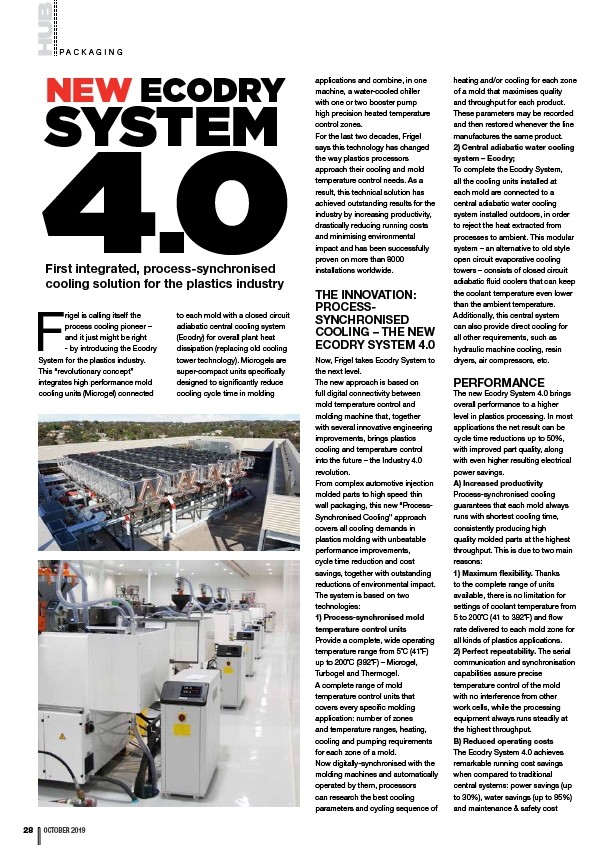
PA C K A G I N G
NEW ECODRY
First integrated, process-synchronised
cooling solution for the plastics industry
Frigel is calling itself the
process cooling pioneer –
and it just might be right
- by introducing the Ecodry
System for the plastics industry.
This “revolutionary concept”
integrates high performance mold
cooling units (Microgel) connected
28 OCTOBER 2019
to each mold with a closed circuit
adiabatic central cooling system
(Ecodry) for overall plant heat
dissipation (replacing old cooling
tower technology). Microgels are
super-compact units specifically
designed to significantly reduce
cooling cycle time in molding
applications and combine, in one
machine, a water-cooled chiller
with one or two booster pump
high precision heated temperature
control zones.
For the last two decades, Frigel
says this technology has changed
the way plastics processors
approach their cooling and mold
temperature control needs. As a
result, this technical solution has
achieved outstanding results for the
industry by increasing productivity,
drastically reducing running costs
and minimising environmental
impact and has been successfully
proven on more than 8000
installations worldwide.
THE INNOVATION:
PROCESSSYNCHRONISED
COOLING – THE NEW
ECODRY SYSTEM 4.0
Now, Frigel takes Ecodry System to
the next level.
The new approach is based on
full digital connectivity between
mold temperature control and
molding machine that, together
with several innovative engineering
improvements, brings plastics
cooling and temperature control
into the future – the Industry 4.0
revolution.
From complex automotive injection
molded parts to high speed thin
wall packaging, this new “Process-
Synchronised Cooling” approach
covers all cooling demands in
plastics molding with unbeatable
performance improvements,
cycle time reduction and cost
savings, together with outstanding
reductions of environmental impact.
The system is based on two
technologies:
1) Process-synchronised mold
temperature control units
Provide a complete, wide operating
temperature range from 5˚C (41˚F)
up to 200˚C (392˚F) – Microgel,
Turbogel and Thermogel.
A complete range of mold
temperature control units that
covers every specific molding
application: number of zones
and temperature ranges, heating,
cooling and pumping requirements
for each zone of a mold.
Now digitally-synchronised with the
molding machines and automatically
operated by them, processors
can research the best cooling
parameters and cycling sequence of
heating and/or cooling for each zone
of a mold that maximises quality
and throughput for each product.
These parameters may be recorded
and then restored whenever the line
manufactures the same product.
2) Central adiabatic water cooling
system – Ecodry;
To complete the Ecodry System,
all the cooling units installed at
each mold are connected to a
central adiabatic water cooling
system installed outdoors, in order
to reject the heat extracted from
processes to ambient. This modular
system – an alternative to old style
open circuit evaporative cooling
towers – consists of closed circuit
adiabatic fluid coolers that can keep
the coolant temperature even lower
than the ambient temperature.
Additionally, this central system
can also provide direct cooling for
all other requirements, such as
hydraulic machine cooling, resin
dryers, air compressors, etc.
PERFORMANCE
The new Ecodry System 4.0 brings
overall performance to a higher
level in plastics processing. In most
applications the net result can be
cycle time reductions up to 50%,
with improved part quality, along
with even higher resulting electrical
power savings.
A) Increased productivity
Process-synchronised cooling
guarantees that each mold always
runs with shortest cooling time,
consistently producing high
quality molded parts at the highest
throughput. This is due to two main
reasons:
1) Maximum flexibility. Thanks
to the complete range of units
available, there is no limitation for
settings of coolant temperature from
5 to 200˚C (41 to 392˚F) and flow
rate delivered to each mold zone for
all kinds of plastics applications.
2) Perfect repeatability. The serial
communication and synchronisation
capabilities assure precise
temperature control of the mold
with no interference from other
work cells, while the processing
equipment always runs steadily at
the highest throughput.
B) Reduced operating costs
The Ecodry System 4.0 achieves
remarkable running cost savings
when compared to traditional
central systems: power savings (up
to 30%), water savings (up to 95%)
and maintenance & safety cost
4.0 SYSTEM