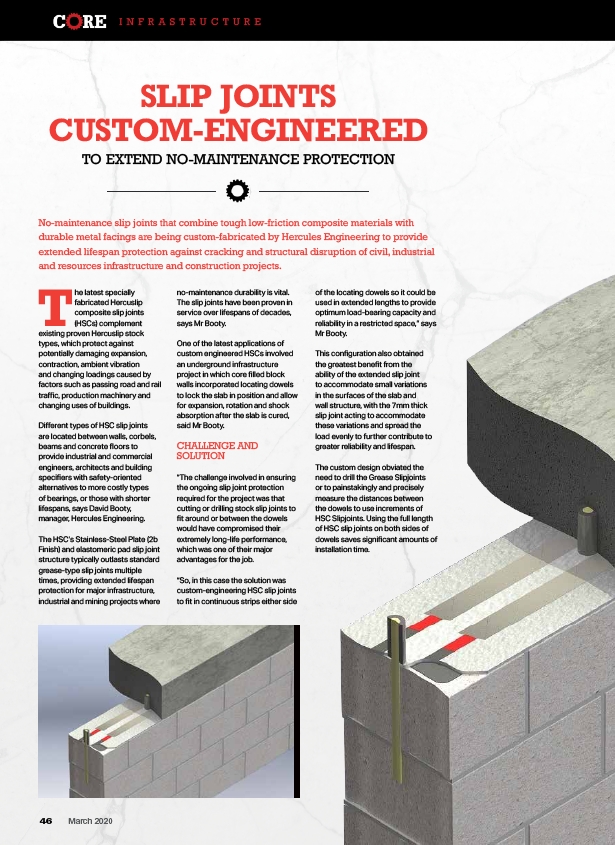
I N F R A S T R U C T U R E
SLIP JOINTS
CUSTOM-ENGINEERED
TO EXTEND NO-MAINTENANCE PROTECTION
No-maintenance slip joints that combine tough low-friction composite materials with
durable metal facings are being custom-fabricated by Hercules Engineering to provide
extended lifespan protection against cracking and structural disruption of civil, industrial
and resources infrastructure and construction projects.
The latest specially
fabricated Hercuslip
composite slip joints
(HSCs) complement
existing proven Hercuslip stock
types, which protect against
potentially damaging expansion,
contraction, ambient vibration
and changing loadings caused by
factors such as passing road and rail
traffic, production machinery and
changing uses of buildings.
Different types of HSC slip joints
are located between walls, corbels,
beams and concrete floors to
provide industrial and commercial
engineers, architects and building
specifiers with safety-oriented
alternatives to more costly types
of bearings, or those with shorter
lifespans, says David Booty,
manager, Hercules Engineering.
The HSC’s Stainless-Steel Plate (2b
Finish) and elastomeric pad slip joint
structure typically outlasts standard
grease-type slip joints multiple
times, providing extended lifespan
protection for major infrastructure,
industrial and mining projects where
no-maintenance durability is vital.
The slip joints have been proven in
service over lifespans of decades,
says Mr Booty.
One of the latest applications of
custom engineered HSCs involved
an underground infrastructure
project in which core filled block
walls incorporated locating dowels
to lock the slab in position and allow
for expansion, rotation and shock
absorption after the slab is cured,
said Mr Booty.
CHALLENGE AND
SOLUTION
“The challenge involved in ensuring
the ongoing slip joint protection
required for the project was that
cutting or drilling stock slip joints to
fit around or between the dowels
would have compromised their
extremely long-life performance,
which was one of their major
advantages for the job.
“So, in this case the solution was
custom-engineering HSC slip joints
to fit in continuous strips either side
of the locating dowels so it could be
used in extended lengths to provide
optimum load-bearing capacity and
reliability in a restricted space,” says
Mr Booty.
This configuration also obtained
the greatest benefit from the
ability of the extended slip joint
to accommodate small variations
in the surfaces of the slab and
wall structure, with the 7mm thick
slip joint acting to accommodate
these variations and spread the
load evenly to further contribute to
greater reliability and lifespan.
The custom design obviated the
need to drill the Grease Slipjoints
or to painstakingly and precisely
measure the distances between
the dowels to use increments of
HSC Slipjoints. Using the full length
of HSC slip joints on both sides of
dowels saves significant amounts of
installation time.
46 March 2020