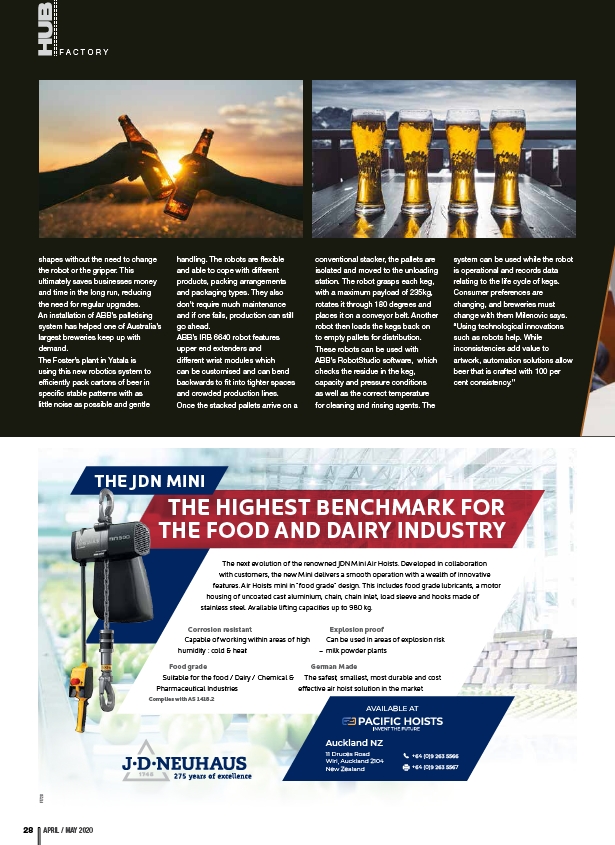
F A C T O R Y
shapes without the need to change
the robot or the gripper. This
ultimately saves businesses money
and time in the long run, reducing
the need for regular upgrades.
An installation of ABB’s palletising
system has helped one of Australia’s
largest breweries keep up with
demand.
The Foster’s plant in Yatala is
using this new robotics system to
efficiently pack cartons of beer in
specific stable patterns with as
little noise as possible and gentle
THE JDN MINI
THE HIGHEST BENCHMARK FOR
THE FOOD AND DAIRY INDUSTRY
The next evolution of the renowned JDN Mini Air Hoists. Developed in collaboration
with customers, the new Mini delivers a smooth operation with a wealth of innovative
features. Air Hoists mini in “food grade” design. This includes food grade lubricants, a motor
housing of uncoated cast aluminium, chain, chain inlet, load sleeve and hooks made of
stainless steel. Available lifting capacities up to 980 kg.
Corrosion resistant
Capable of working within areas of high
humidity : cold & heat
Food grade
Suitable for the food / Dairy / Chemical &
Pharmaceutical Industries
Explosion proof
Can be used in areas of explosion risk
– milk powder plants
German Made
The safest, smallest, most durable and cost
effective air hoist solution in the market
Complies with AS 1418.2
AVAILABLE AT
Auckland NZ
11 Druces Road
Wiri, Auckland 2104
New Zealand
+64 (0)9 263 5566
+64 (0)9 263 5567
FT728
handling. The robots are flexible
and able to cope with different
products, packing arrangements
and packaging types. They also
don’t require much maintenance
and if one fails, production can still
go ahead.
ABB’s IRB 6640 robot features
upper end extenders and
different wrist modules which
can be customised and can bend
backwards to fit into tighter spaces
and crowded production lines.
Once the stacked pallets arrive on a
conventional stacker, the pallets are
isolated and moved to the unloading
station. The robot grasps each keg,
with a maximum payload of 235kg,
rotates it through 180 degrees and
places it on a conveyor belt. Another
robot then loads the kegs back on
to empty pallets for distribution.
These robots can be used with
ABB’s RobotStudio software, which
checks the residue in the keg,
capacity and pressure conditions
as well as the correct temperature
for cleaning and rinsing agents. The
system can be used while the robot
is operational and records data
relating to the life cycle of kegs.
Consumer preferences are
changing, and breweries must
change with them Milenovic says.
“Using technological innovations
such as robots help. While
inconsistencies add value to
artwork, automation solutions allow
beer that is crafted with 100 per
cent consistency.”
28 APRIL / MAY 2020