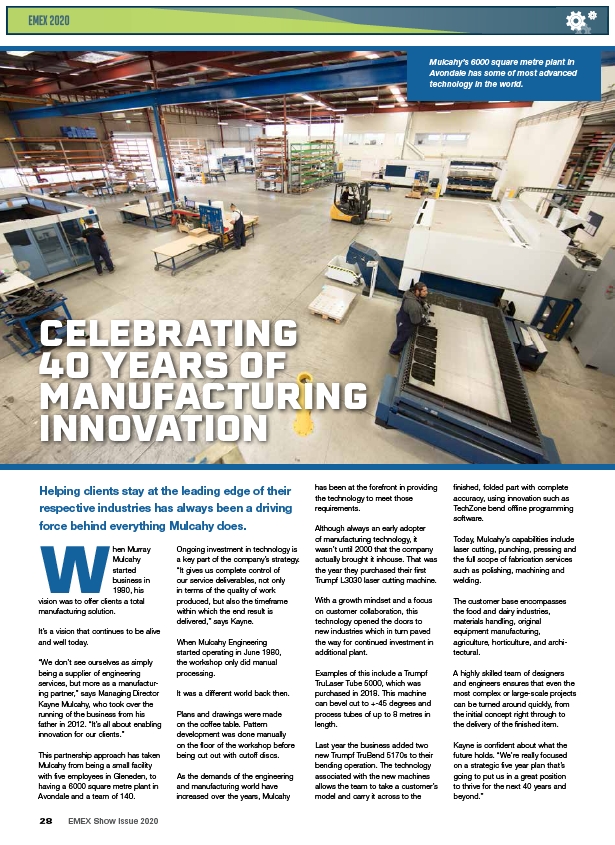
EMEX 2020
CELEBRATING
40 YEARS OF
MANUFACTURING
INNOVATION
When Murray
Mulcahy
started
business in
1980, his
vision was to offer clients a total
manufacturing solution.
It’s a vision that continues to be alive
and well today.
“We don’t see ourselves as simply
being a supplier of engineering
services, but more as a manufacturing
partner,” says Managing Director
Kayne Mulcahy, who took over the
running of the business from his
father in 2012. “It’s all about enabling
innovation for our clients.”
This partnership approach has taken
Mulcahy from being a small facility
with five employees in Gleneden, to
having a 6000 square metre plant in
Avondale and a team of 140.
Ongoing investment in technology is
a key part of the company’s strategy.
“It gives us complete control of
our service deliverables, not only
in terms of the quality of work
produced, but also the timeframe
within which the end result is
delivered,” says Kayne.
When Mulcahy Engineering
started operating in June 1980,
the workshop only did manual
processing.
It was a different world back then.
Plans and drawings were made
on the coffee table. Pattern
development was done manually
on the floor of the workshop before
being cut out with cutoff discs.
As the demands of the engineering
and manufacturing world have
increased over the years, Mulcahy
has been at the forefront in providing
the technology to meet those
requirements.
Although always an early adopter
of manufacturing technology, it
wasn’t until 2000 that the company
actually brought it inhouse. That was
the year they purchased their first
Trumpf L3030 laser cutting machine.
With a growth mindset and a focus
on customer collaboration, this
technology opened the doors to
new industries which in turn paved
the way for continued investment in
additional plant.
Examples of this include a Trumpf
TruLaser Tube 5000, which was
purchased in 2018. This machine
can bevel cut to +-45 degrees and
process tubes of up to 8 metres in
length.
Last year the business added two
new Trumpf TruBend 5170s to their
bending operation. The technology
associated with the new machines
allows the team to take a customer’s
model and carry it across to the
finished, folded part with complete
accuracy, using innovation such as
TechZone bend offline programming
software.
Today, Mulcahy’s capabilities include
laser cutting, punching, pressing and
the full scope of fabrication services
such as polishing, machining and
welding.
The customer base encompasses
the food and dairy industries,
materials handling, original
equipment manufacturing,
agriculture, horticulture, and architectural.
A highly skilled team of designers
and engineers ensures that even the
most complex or large-scale projects
can be turned around quickly, from
the initial concept right through to
the delivery of the finished item.
Kayne is confident about what the
future holds. “We’re really focused
on a strategic five year plan that’s
going to put us in a great position
to thrive for the next 40 years and
beyond.”
Helping clients stay at the leading edge of their
respective industries has always been a driving
force behind everything Mulcahy does.
Mulcahy’s 6000 square metre plant in
Avondale has some of most advanced
technology in the world.
28 EMEX Show Issue 2020